New demands on PCB fabrication, namely advanced packaging, ultra high density interconnect (UHDI), and new specialty materials, are converging, changing the landscape of our business. Is it time to start paying close attention to this convergence?
A solid strategy is a critical part of success. This month, we asked some of the top industry leaders and business strategy “gurus” to share their thoughts on developing strategies. Printed Board
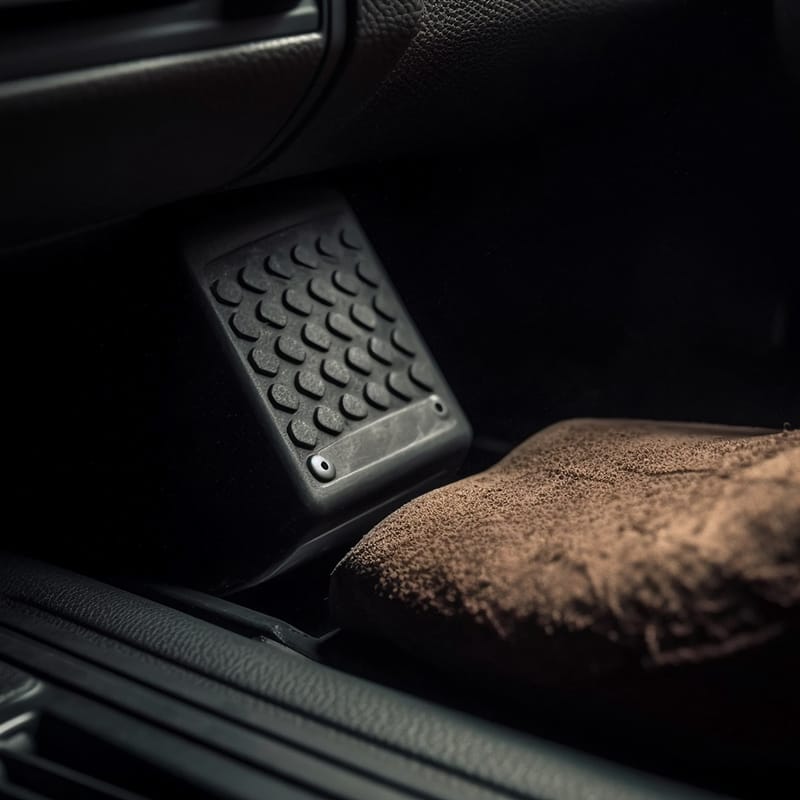
In this issue, we explore how TQM has entered the DNA of continuous improvement disciplines, and the role leadership transformation plays in this. If you've ever competed against a TQM company, you understand their winning advantage.
Editor’s note: The following is an excerpt from Chapter 1 of The Printed Circuit Designer’s Guide to... Producing the Perfect Data Package written by Mark Thompson of Prototron Circuits.
Deciding on the class of the final product will determine what files are needed for fabrication and assembly. It is critical to note that for a product to be built to any class level, it must be designed to that class level from its inception.
Let’s review the various PCB classes as defined by IPC—Association Connecting Electronics Industries. IPC is the trade association for the electronics industry that provides standards, training and certification, market research, education, and public policy advocacy to support all facets of the industry, including design, PCB manufacturing, and electronics assembly.
First, understand that IPC has different specifications depending on the PCB type. This book will address rigid and rigid-flex PCBs. The industry standards for these PCB types are:
• IPC-6012: Qualification and Performance Specification for Rigid Printed Boards
• IPC-6013: Qualification and Performance Specification for Flexible Printed Boards
• IPC-6018: Qualification & Performance Specification for High Frequency (Microwave) Printed Boards
• IPC-6012DS: Space and Military Avionics Applications Addendum to IPC-6012D: Qualification and Performance Specification for Rigid Printed Boards
There are three different board classes as defined by IPC-6012 and IPC-6013. The appropriate class will be defined by the criticality of the product the PCB will be integrated with.
Class 1 is for “general electronic products” and is the lowest reliability class. Therefore, it requires the least amount of additional information in a fabrication package to meet product reliability. For instance, a Class 1 or Class 2 PCB does not require a netlist compare, whereas Class 3 and Class 3A do require it. Thus, for a Class 1 or Class 2 part, if IPC netlists and any instructions expressing the need for a net compare are not provided, a separate netlist file is not required in the output package.
Class 2 is for “dedicated service products” and requires a little more information to be provided, as continued performance and extended life cycle are required. Uninterrupted service is not mandatory for Class 2 PCBs. It is important to note that while a Class 2 PCB does not require an IPC netlist be provided to do a design versus exported image data comparison, it is highly recommended as part of the output package.
Class 3 is specified for the highest reliability and continued high performance in segments where equipment failure simply cannot be tolerated, such as the medical or aerospace industries. For IPC 6012 Class 3 an IPC netlist comparison is required. Netlists typically follow IPC-D-356, IPC-D-356A, or a Mentor neutral file. Other older forms of IPC netlists can be used if a fabricator has the ability to use raw computer-aided design (CAD) data, but by far the most common formats for fabrication are the three previously mentioned.
As a fabricator, we constantly see PCBs called out as IPC-6012 Class 3 that have not been designed to meet Class 3 requirements, such as minimum annular ring or clearance (Figure 1.1). If the PCB was not designed to meet Class 3 requirements, the fabricator does not have a chance to provide the customer with a Class 3 PCB. Designers should use the IPC-2220 series of documents concerning board design and fabrication to ensure a design-to-fabrication match.
Part sizes are shrinking while part densities are growing, which reduces space and makes it increasingly difficult to have enough supporting annular ring or clearance. One way to minimize delays in the fabrication quote or manufacturing process is to qualify this by saying the product is to be built to IPC-6012 Class 3 with an allowance for annular ring and clearance to Class 2. This may preclude a phone call from your fabricator to tell you the quote is on hold because the design does not meet Class 3 minimum annular ring requirements (Figure 1.1).

Led Pcb Assembly To read the ebook, The Printed Circuit Designer’s Guide to... Producing the Perfect Data Package, click here.