Synopsis: Cellular PVC is a common building material, but is relatively new as a siding. This article discusses the wood-like look of cellular PVC siding as well as the durability and resiliency benefits in areas with weather events, as well as specifics of one brand of siding’s interlocking joints and installation process.
Carpenters have used cellular PVC trims for decades, but as a solid and practical siding, cellular PVC cladding is a recent development. I first saw cellular PVC siding in its early stages when building-product manufacturer Westlake Royal asked me to organize a private meeting with architectural thought leaders Steve Mouzon and Andrés Duany. These two architects are well known for their critique of vinyl siding, and the manufacturer wanted their honest opinion on a new category of PVC cladding. While the architects scrutinized and complimented the clean lines, crisp edges, and rigidity, I was fascinated by the rabbeted, interlocking ends and the notion that any plastic siding could withstand 210-mph winds. House Wall Exterior
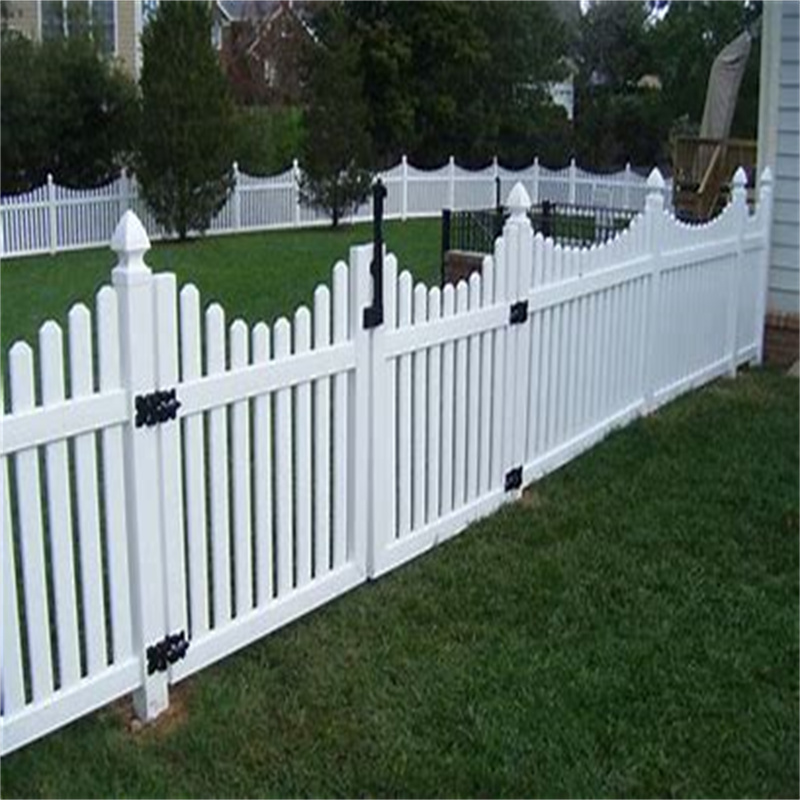
In the building world, cellular PVC is a solid plastic material, and it has been used for nearly three decades as a 100% synthetic alternative to traditional wood trim. “PVC” stands for polyvinyl chloride, the same material used for DWV pipes as well as vinyl siding (and many other building products). Cellular PVC is a type of polyvinyl chloride that is softer and more flexible than standard PVC. This softness means that cellular PVC can be molded to resemble real wood without feeling like plastic.
While not all vinyl is PVC, all PVC is vinyl, and the majority of vinyl products you encounter in the building world are made from PVC. PVC materials include additives that make them stronger, more durable, and more resistant to UV exposure and weather than other plastics. This is why PVC performs well as siding.
Cellular PVC siding as we know it has been around for about fifteen years. It’s primarily used along the eastern seaboard because of properties that make it ideal for coastal climates, though its popularity is growing in the Midwest and South because of its durability.
The biggest adjustment to working with cellular PVC siding is the order of installation. Unlike other siding materials, PVC siding is installed before the trim. The first step is to install furring strips or spacers around openings and inside and outside corners using 1×2 PVC or treated wood. Next, install the siding, allowing a 1/2-in. to 1-in. gap between the boards and furring strips—a full inch if the run is 12 ft. or longer, and 1/2 in. if shorter. PVC claddings need room to move as a result of changes in temperature, and this gap enables that to happen.
Any cellular PVC siding needs to solve for the issue of thermal movement at the butt joints. During the seasonal fluctuation of summer and winter, PVC may expand and contract as much as 1/2 in. within a 12-ft. span. Manufacturers take different approaches to locking butt joints together and accommodating thermal movement. The Westlake Royal Celect Cellular Composite Siding installed on this project uses a rabbeted joint tooled into the ends of each board. Gripping like interlocking fingers, this machined joint causes the run of siding to move as one piece from end to end. And because the rabbeted union is precise, the seams virtually disappear. Expansion occurs at both ends of panel runs, with trim pieces covering any movement at corners and around windows and doors. This method of interlocking makes the siding very resilient once installed. Each piece of siding is fully secured on all four sides, giving it unbeatable strength, especially against strong winds and storm conditions.
(For more, see Prefabricating Exterior Window Trim, FHB #260)
As prices rise for other types of synthetic siding, cellular PVC’s up-front cost has fallen more in line with that of its competitors. While cellular PVC is still priced higher than fiber cement, its installation cost can be significantly lower, making it an attractive alternative. And like traditional vinyl siding, it’s prefinished, low maintenance, and available in many colors. (See a side-by-side comparison at the bottom of this page, with material prices from my local dealer.)
Many homeowners want the look of wood siding, but not the price tag and maintenance. Vinyl siding accomplishes both objectives for a low-cost installation, but cellular PVC looks, feels, and acts more like wood. It’s available in several profiles for a more customized exterior, including traditional clapboards with a smooth or wood-grain finish as well as shakes and vertical boards and battens. It looks convincingly like painted wood siding, installs with standard woodworking tools and techniques, and lasts a long time without maintenance. Most cellular PVC siding is warranted for at least 25 years.
With a cellular PVC siding installation, the boards stack on top of one another, interlocking horizontally. The nail hem provides oblong slots to center fasteners. This built-in water management allows the material to move and breathe and creates a rainscreen cavity behind the siding large enough to drain via gravity. Because the joints of the siding aren’t airtight, the wall assembly behind the siding can dry to the exterior. PVC absorbs no moisture, so it can scribe along a roof edge or remain in contact with the ground without causing damage to the substrate or finish.
PVC is among the most easily recycled plastics because of its simple composition—it’s made of just one plastic as opposed to a combination of many. As an embedded plastic installed on a house (not a single-use plastic that is discarded quickly, such as a water bottle), it does not readily pollute the environment. And though recycling used PVC building materials is still a challenge in many parts of the country, the manufacturing process for vinyl products yields virtually no waste.
The low global warming potential of vinyl products makes cellular PVC an attractive cladding alternative to brick (which may have a longer useful life but has a heavier up-front carbon footprint). If up-front carbon reduction and long-lasting siding are a priority, wood and vinyl claddings (including cellular PVC) are good options. And cellular PVC lasts longer and is more durable than traditional vinyl siding.
If a woodlike aesthetic is the goal, cellular PVC siding is an approachable and increasingly affordable alternative. I am convinced that solid, cellular PVC claddings—which are resilient, durable, and almost impervious to wind and hail—will become increasingly popular as one of the best material choices available when balancing performance and price.
Fernando Pagés Ruiz is a builder and an ICC-certified residential building inspector in Houston. Photos by the author, except where noted. Drawings: John Schreiner.
Sign up for eletters today and get the latest how-to from Fine Homebuilding, plus special offers.
The big failure with this article is the lack of consideration for fire and what happens with this siding. When vinyl burns, it is extremely toxic to human (and any other) life. Even melting of the siding puts of gasses you do not want to take in.
Additionally, there is the fire resistance that should be considered in any siding application today. With homes in cities being placed closer and closer together, when one goes most often so do the ones on either side of them.
I get what all the other benefits are, but I just don't see the risk being worth it when we are trying to build greener and greener. This article is so counter to the push I have heard (and appreciate) from this publication, even when I work in the Oil & Gas sector.
I am sorry I did not see your comment sooner. Vinyl does not burn until it approaches 730°F (387°C) and will not self-ignite until 850°F (454°C). House fires burn at about 530°F (260°C). The material will melt but not ignite and contribute to the fire. Unless you use vinyl indoors (as they do at the Apple Store and other commercial interiors), I don't see how the toxicity would have a dangerous effect--people don't usually stand around a burning house and take deep breaths. There is no restriction on using vinyl indoors. Many products do. At the same time, restrictions exist for material that off-gas dangerous toxins when burning, such as many rigid foam boards. Even if you have a fire lapping at the siding at the nearly 700°F you would need for vinyl to burn, the toxic potency of vinyl would not be considered to be any different from that of wood when burning, since all burning materials release highly toxic smoke.
The most important toxic product in any fire is carbon monoxide (CO), which is produced by all organic compounds as they burn. Vinyl releases less CO than most wood products, and as such its contribution to overall toxicity in a house fire is negligible (according to NIST Radiant Toxicity Test Results).
Of course, and again, this only matters if you install vinyl siding on interior walls. On exterior walls, the net toxicity of vinyl siding in a fire is virtually zero. To get into the science, I refer you to a commonly referenced authoritative document, Casarett & Doull’s “Toxicology – The Basic Science of Poisons.”
Trusted, comprehensive guidance from the pros for choosing, installing, and repairing siding and exterior trim
View All Project Guides »
Become a member and get unlimited site access, including the Siding & Exterior Trim Project Guide.
Get home building tips, offers, and expert advice in your inbox
© 2023 The Taunton Press, Inc. All rights reserved.
Get home building tips, offers, and expert advice in your inbox
Become a member and get instant access to thousands of videos, how-tos, tool reviews, and design features.
Start your subscription today and save up to 70%
Get complete site access to expert advice, how-to videos, Code Check, and more, plus the print magazine.
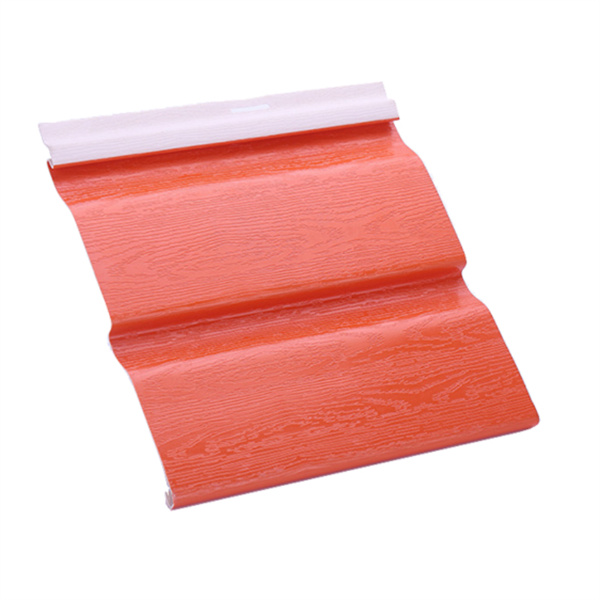
Outdoor Pvc Paneling Already a member? Log in