by RYAN JORGENSEN, Senior Application Engineer, JNT Technical Services Inc.
Heat exchanger tube plugs are used to seal leaking heat exchanger tubes, thus preventing damage to adjacent tubes and keeping the efficiency on an aging exchanger as high as possible. Condenser Copper Coil
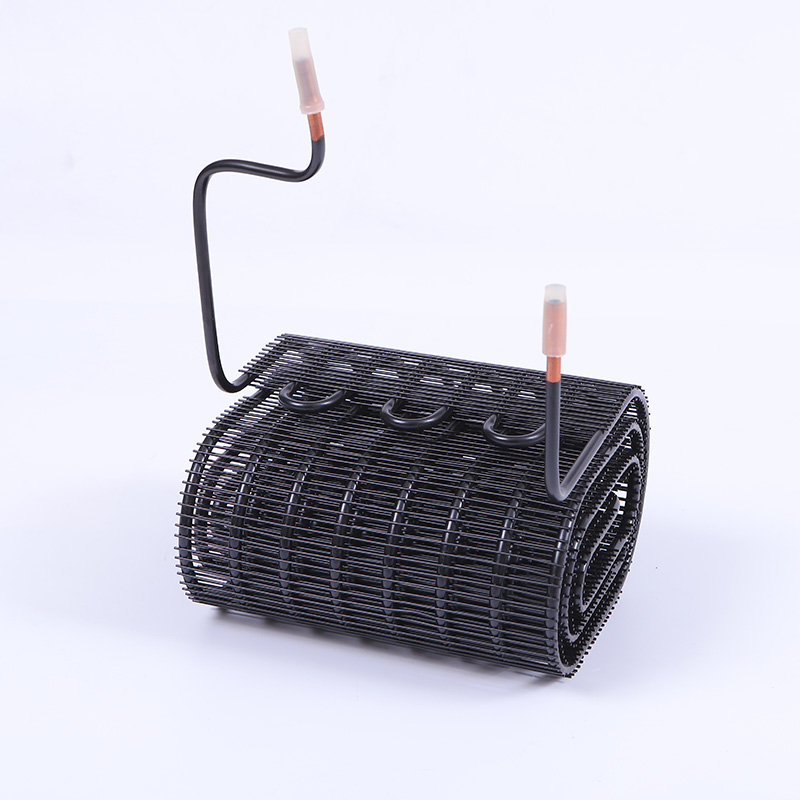
Torq N' Seal® Heat Exchanger Tube Plugs offer a fast, simple and effective way to seal leaking heat exchangers up to 7,000 psi. Whether you have a feedwater heater, lube oil cooler, condenser or any other type of heat exchanger, knowing how to properly seal a leaking tube will improve turnaround time, reduce project cost and ensure the longest possible asset life.
There are several ways to identify heat exchanger tube leaks, including the pressure leak test, vacuum leak test, eddy current test, hydrostatic test, acoustic test and radiotracers to name a few. The proper method for a given heat exchanger depends on the service requirements associated with that exchanger. For instance, a critical feedwater heater often needs to be plugged based on minimum wall thickness before a leak even occurs. For these applications, eddy current testing or acoustic testing will be the best options. On the other hand, an array of condensers with significant over-capacity can withstand a certain number of leaking tubes without affecting the process. In this case, vacuum or pressure testing are the best options for their low cost and ease of use.
Now that all tube leaks (or tubes with thin walls below the minimum allowed thickness) have been identified, it is time to begin the tube plugging process. The first step is to remove any loose scaling or corrosive oxides from the tube's inner diameter surface. Use a slightly oversized, hand-operated tube brush or put some emery cloth on your finger. Gently maneuver the brush or cloth inside the tube, removing any loose material. Two to three passes are enough; the goal is just to remove loose material not to resize the tube.
Next, confirm your tube size by measuring the tube inside diameter with a 3-point micrometer or standard caliper. If you use a caliper, take at least three readings and average them together to get the effective inner diameter. Use even more measurements for the average if you only have a ruler. Confirm the measured diameter matches the design diameter from the U1 datasheet or heat exchanger nameplate. Also confirm the tube material at this time; it should also be listed on the U1 datasheet or exchanger nameplate.
Select the correct tube plug
At this point you have the leaking tubes identified, lightly cleaned and the size and material confirmed. Now it is time to select the correct heat exchanger tube plug:
Step 1: Take your measured tube ID and round down to the nearest ten thousandth.
Remove the preceding "0" and decimal point.
Installing the heat exchanger tube plugs
Set your 3/8 inch square drive torque wrench to the recommended installation torque listed on your Torq N' Seal plug box. Affix the Hex Capture Driver (supplied with every box of plugs) to the torque wrench. Then affix the Torq N' Seal plug to the Hex Capture Driver. Insert the plug into the tube so the back of the screw is even with the tube sheet face. Rotate slowly clockwise until the torque wrench clicks. Pull the hex capture drive free. Fast, simple and effective - seal tubes reach up to 7,000 PSI in under 30 seconds with Torq N' Seal Heat Exchanger Tube Plugs.
For more information, visit jnt-tech-serv.com, call (201) 641-2130, or email sales@torq-n-seal.com.
by RYAN JORGENSEN, Senior Application Engineer, JNT Technical Services Inc.
Connecting people in business and industry with one another for the betterment of all. Become a BIC Alliance Member today.

Condenser Ref Copyright © 2023 BIC Alliance, Inc. All rights reserved.