To achieve high-quality pellets at the end of the recycling process, chose filtration technology based on both the input materials as well as the performance requirements of the finished material. #bestpractices #sustainability
Melt filters are a critical component in plastics recycling systems as they remove contaminants such as paper, cardboard, wood, rubber, aluminum or even foreign plastics from the stream. To achieve high-quality pellets at the end of the recycling process, the right filtration technology should be chosen based on both the input materials as well as the performance requirements of the finished pellets. Fabric Wire Cloth
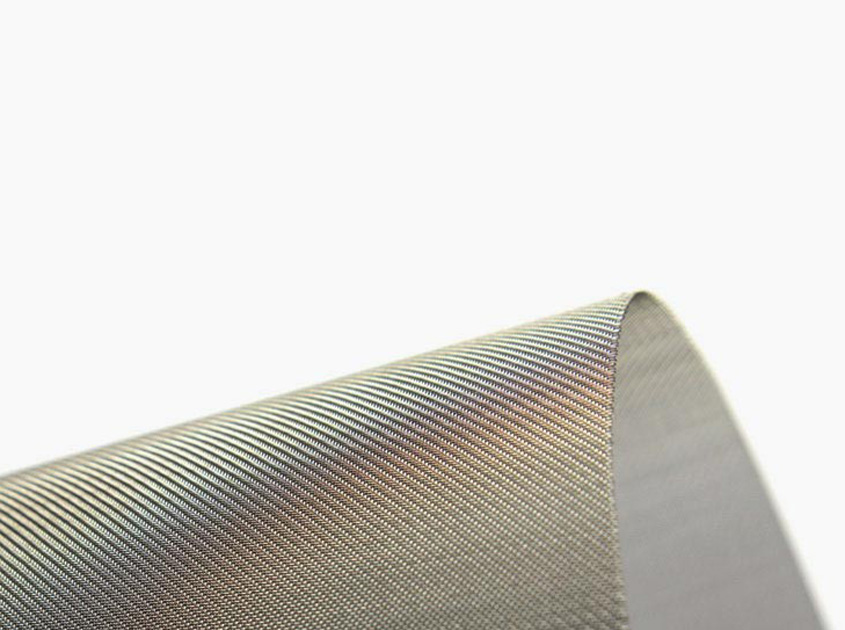
Essentially there are two proven filtration designs: automatic back flushing filters utilizing wire mesh screens and self-cleaning continuous filters that use steel screen discs.
For wire mesh filters, piston screen changer systems with back flushing are used. Each piston carries two filter cavities into which the wire mesh screen packages are inserted. This system enables a cyclical process that provides filtration options in mesh sizes as small as 32 microns and below in some cases.
Since the filter is made from woven wires, it provides high porosity, allowing for a high proportion of open area per unit of surface area. Wire mesh filter system options can start with one piston and two screens for low throughput requirements and go up to 6 pistons and 12 screens for higher throughputs. In order to ensure the stability and continuity of the recycling process with the 6-piston screen changer, the melt pressure difference during the backflush cycle is extremely low; only one out of 12 screens is in backflush mode while the other 11 screens are in full production.
Piston screen changers are a well-proven design for reliable filtration with very fine screens at low differential pressures.
Screen disc filters feature a special steel plate, manufactured to a high specification for hardness, in which the filtration orifices are manufactured with a laser for optimal precision; hence the product name laser filter. While the recycling melt is passing through the holes, the contaminants remain on the screen surface. As these contaminant build up, the melt pressure increases until the system actuates the filter’s scraping mechanism.
Each screen features three scrapers that wipe the screen to free the filtration holes in order to maintain melt flow. This process ensures a very high proportion of open area that enables a high throughput even with very highly contaminated materials.
Laser filters are known for continuous filtration at very stable pressure levels for uninterrupted periods of operation lasting many days or weeks. They also provide a very short residence time of the contaminants on the filter media compared to mesh screen filters where the particles must wait for the next backflush.
Analyzing what kind of contaminants are in your material stream and optimizing the filtration solution accordingly are keys to success.
By contrast, laser filter screens are wiped continuously by the scrapers. The filtration screens can go as small as 70 microns, although in many cases a direct comparison of mesh filters and laser filters shows that the laser filter screen provides a better-defined hole-geometry, due to the manufacturing precision provided by the laser, which in turn delivers a better classification efficiency.
FIG 1 Coming from the extruder, the contaminated plastic melt flows via a circular distributor ring into the housing between two parallel configured laser-drilled screen discs.
FIG 2 The melt is pressed through the screen discs; flows through and leaves the filter in a clean state via the collection channel.
FIG 3 The contaminant particles collect on the screen as the melt flows through. A scraper disc with three scrapers on each side rotates between the screen discs. The pressed on scrapers lift the contaminants immediately from the smooth, hardened screen discs and forward them directly to the discharge system.
The level of contaminants in the plastic stream leads to the decision whether cyclical filtration (i.e. wire mesh filter systems—the piston screen changer) is sufficient (typically valid for contamination levels of up to approx. 0.05%) or if continuous filtration is required; laser filters can process contamination levels of 3-5%.
Analyzing what kind of contaminants are in your material stream and optimizing the filtration solution accordingly are keys to success.
The type of contaminants and to what degree they need to be filtered out will drive decisions about processing (pressure, temperatures) and filtration levels. It makes a significant difference if there are mainly particles to be filtered that are dimensionally stable at the point where they contact the filter media (such as wood, for example) or if there are soft particles (as can be seen with foreign plastics, especially if the melting points are not too far apart).
For example, if soft contaminants are involved, then it is essential that the differential pressure is kept low and the residence time at the filter surface kept short in order to avoid the soft particles being squeezed through over time. The performance of the filtration system can be significantly impacted, positively or negatively, by the overall process.
An extruder on its own is typically enough to deliver the melt through the filter; as long as it can deliver sufficient pressure at the required throughput level. If not, then a melt pump may also be required. It will also help the melt filter if the extruder keeps the contaminants large enough by using soft shearing during melting, or if this is not the target, the extruder should include homogenization before the melt filter. Both configurations are possible and it makes sense to consider all the options and the different components involved.
Every intervention by the operator carries the potential for human error, in addition to adding operational cost. The bigger a recycling line is, the more essential it is to achieve a stable and reliable process. Piston screen changers and laser filters have been developed for post-consumer recycling lines where material preparation, sorting and washing systems are upstream of the extrusion process. For such integrated plants, reliability is critical. Because of their robust designs, these systems will help achieve long-term efficiency in the filtration process with virtually any demanding recycling application.
Rather than relying on operators to be involved in adjusting the system, an advanced filter adjusts itself automatically. Filter systems should also not require a shut-down of the extruder but allow for filter changes while the extruder keeps working. This kind of system has been referred to as a lock- and-change unit because it features a valve system that allows the laser filter screen to be changed on one filter head while the other filter is in full production.
The bigger a recycling line is, the more essential it is to achieve a stable and reliable process.
Simplicity and a robust design are important criteria because the melt should flow through the system without dead spots or material hang ups. Melt filtration systems can be equipped with screens that have large surface areas to prevent pressure spikes, the filters are easily accessible so that they can be reached quickly, and our intuitive HMI helps the operator to interact with the system. Any wear components in the system are easily accessible to minimize down time and eliminate complex training requirements for operators.
Due to the myriad of different systems and component combinations, it is a challenge to find a universal filtration solution. Discussion, sharing experience with others and ultimately, testing a melt filtration system in a trial run with the customer's specific input materials and resin requirements, will enable an informed decision in the end.
About the Author: After attending engineering college and subsequent years of technical experience, Robert Obermayr graduated in law at the Johannes Kepler University in Linz, Austria, in 2002. Following several years of working as a commercial project manager for a steel plant engineering company, he was responsible at Erema for the product Corema, a system for recycling and compounding in one processing step. In 2017, he became head of Erema’s business unit Powerfil. Contact: r.obermayr@erema.at
Plenty of companies are taking advantage 3D printing’s disruptive nature in the manufacturing space, but I came across an Amsterdam-based startup that is taking the disruptive concept even further.
Blazing speed plus shrinking energy consumption supported the “green” theme at the big show. Smarter controls and growing connectivity were another key focus.
This new aggregate—consisting of 80% waste plastic and 20% organic additive—is designed to mix with cement.
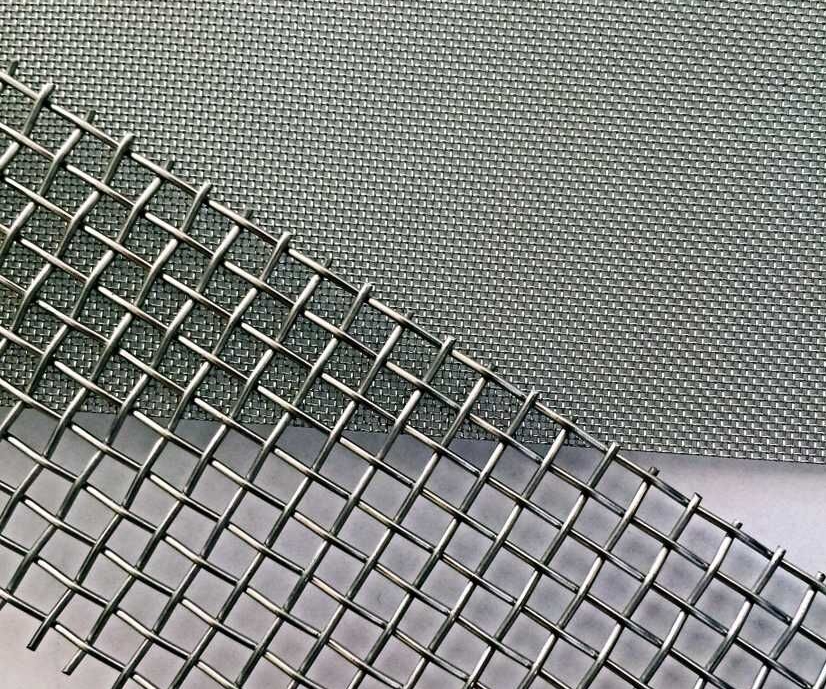
Copper Wire Mesh Roll © 2023 Gardner Business Media, Inc. Privacy Policy [Log On]