Compressor technology has been evolving since the earliest days of air conditioning; the time has come to embrace the latest generation.
It was one spring day in the mid-1970’s that I tagged along with an experienced refrigeration technician on a residential service call. My task that day, as a neophyte helper, was to carry tools and equipment in and out of a fabulous mansion located just north of downtown Toronto. Automatic Line Series

In those days, residential air conditioning consisted mainly of table fans, strategically opened windows and, for some, the emerging window air conditioner market helped to provide relief from Toronto’s notorious summertime heat and humidity.
When I first entered the mechanical room of this home, I stood in awe at the size and complexity of the equipment.
An enormous oil furnace had two slab cooling coils installed in series in the hot air plenum, both on a 45-degree angle with each controlled by an adjustable TXV.
The furnace had a massive two-speed motor running in continuous mode year-round. Part of our job was to lubricate the motor, change the drive pulley and belt, and electrically switch the motor into continuous high speed for the summer cooling airflow requirement.
I really fell in love with the two water-cooled serviceable hermetic compressors mounted on springs attached to heavy steel I-beams. Next to them, mounted on the side wall, were two huge motor starters containing a bunch of capacitors and other controls; I couldn’t wait to learn all about it.
An era is often defined as a period of time marked by distinctive character. Never again did I see a serviceable or semi-hermetic compressor in a residential application, because shortly after that fateful day the first residential split system air conditioning units arrived in my expanding HVAC world.
Several of the earliest splits I encountered used rotary compressors; these are positive displacement compressors using a rolling piston or rotating vane that have the advantage of providing constant flow of suction and discharge gases and are still used today in various applications.
Positive displacement reciprocating compressors, also known as piston compressors, are essentially pumps that provide—as all refrigerant compressors do—a pressure differential allowing refrigerant to flow.
By adding heat during the pumping process vapour pressure is increased to the high side condition. Hermetic compressor manufacturers developed several reciprocating designs for use in residential applications. One such design had four opposing pistons arranged on a flat plane.
Another design incorporated capacity control by using two pistons. Under low load only one piston pumped, and when greater capacity was required the motor would reverse and engage the second piston thus providing full pumping capacity.
In the 1950’s, General Electric developed a reciprocating compressor meant for cooling and heat pump applications. The compressor had a unique valving system allowing for a minuscule clearance volume: on every discharge stroke of the piston almost all the charge was pushed out of the cylinder thus improving pumping efficiency. The over-sized hermetic shell served as a refrigerant accumulator featuring a loop of discharge tubing running through the bottom of the shell.
The hot discharge line would vaporize any liquid refrigerant finding its way back to the compressor during operation. The all-aluminum frame, motor housing, piston and connecting rod components were designed to reduce thermal stress and to help the compressor to run cooler by dissipating heat away from bearing surfaces. Truly a unique concept, many reciprocating compressors of this type are still in use today.
By 1987, the Trane Company had introduced its 3D Scroll compressor to the commercial marketplace, although Trane was one of the last manufacturers to use scrolls in residential products. While reciprocating compressors continue to enjoy an excellent record of reliability, the improved efficiency, reduced noise levels, and the much lower cost of production inevitably convinced split system manufacturers to fully embrace scroll compressors in most of their product offerings.
Scroll compression volume is formed by the orbiting relationship between the two involutes that compress the refrigerant gas in a continuous circular motion. As the orbiting scroll moves, it creates a decreasing volume between itself and the stationary scroll. Refrigerant gas is drawn into the pockets between the two scroll involutes, and as the orbiting involute continues to move the pockets become smaller and smaller eventually forcing the compressed gas through the center port and along to the condenser coil.
Without having to worry about a piston colliding with the cylinder head or valve assembly, there is no clearance volume to reduce compression efficiency.
The scroll set incorporates mechanisms that allow for radial and axial conformance: the involutes can move up and down or side to side just enough to allow a small amount of liquid to pass through without damaging the assembly. (Note: small amount!)
Figure 1. Scroll compressor with a modulation ring incorporated into the scroll set. (source: Copeland)
In the early 2000’s, scroll compressors with a modulation ring incorporated into the scroll set (Figure 1) were introduced into the premium equipment segment and became known as two-step compressors having pumping capacity reduced by 35% in first step.
Two-step scroll outdoor units connected to variable speed air handlers not only offered some energy savings, but consistent temperatures and better humidity control.
Intense governmental scrutiny of energy using appliances such as gas furnaces, refrigerators, air conditioners and heat pumps (to name just a few) pushed manufacturers to find more substantial ways of reducing watts consumed by these products while delivering the same level or even better performance.
Partial capacity control offered by two-step scrolls was bettered by the introduction of the variable frequency drive, also known as the inverter drive, to residential HVAC over a decade ago.
Inverters control the speed of the compressor by adjusting the frequency of the supplied electrical power rather than using mechanical unloading devices to deliver improved low load efficiency and better humidity control all while using fewer watts while only partially loaded.
An inverter drive takes the incoming AC voltage and converts it to DC using a rectifier. The resulting DC voltage powers the inverter circuit that produces an AC voltage at variable frequency.
The compressor motor speed is controlled by the AC hertz delivered to it depending upon the heating or cooling load conditions. Inverter drives, combined with the recent introduction of dense vapour injection, or flash injection, of refrigerant directly into the scroll set made the cold climate heat pump a truly revolutionary advancement in our industry.
Early scroll compressors tended to vibrate a bit too much, and some were even noisier than recips of the day. I remember reading an article published by one manufacturer in the early days saying that scroll compressors were unsuitable for use in residential applications less than 42K Btu/h. Although those teething problems were eventually satisfactorily attenuated, scrolls have another tendency that some electricity distribution utilities in Canada are very upset about.
Figure 2. Note the starting lock rotor amperage (LRA) printed on this compressor name plate.
It has to do with rapid voltage changes caused by high current consumption during the start-up of residential heat pumps having compressors with lock rotor currents capable of drawing more than 100 amps (see Figure 2).
Too many large conventional air conditioners or heat pumps starting a cycle at roughly the same time will create a significant voltage drop that can affect the stability of the electrical grid.
Homeowners recognize this voltage drop as light flicker, one utility reported that 7% of their customer complaints last year resulted from light flicker.
You often hear comments portraying our electric distribution grid as old and creaky; no doubt, many improvements must be made to support the level of electrification so many of us want.
Utility engineers are working toward fortifying the distribution system by increasing secondary network conductor size, increasing service conductor size, and increasing transformer size among other things. However, larger transformer installations must be balanced with demand because transformers work most efficiently at ~80% capacity. Thus, utilities are looking for appliance manufacturers to improve the electrical/electronic characteristics of residential and commercial HVAC/R equipment that can potentially pollute the grid with transients, harmonics, voltage sags and surges.
Inverter driven compressors typically require only 30% to 40% lock rotor current at start-up. Inverters often incorporate an automatic function that supplies active power factor correction designed to boost DC output voltage to the compressor when power demand is high.
Such power correction improves the power factor for the local electrical utility by reducing current draw and, at the same time, limiting harmonic distortion that may lead to the utility transformer overheating.
But inverter driven compressors can also be the victims of power quality issues, the very same voltage fluctuations and surges potentially caused by their neighbouring conventional compressors creating mayhem on the grid.
Inverter controls can be more susceptible to overheating or heat-driven component failures when poor design or low-quality components such as microprocessors, capacitors and semiconductors fail to properly regulate the compressor speed and control system functions.
Figure 3. Note the refrigerant cooled heat sink keeping this unit’s electrical components cool.
Even the best components will generate heat during operation, and without adequate cooling mechanisms such as fans, heat sinks or refrigerant cooled heat sinks (see Figure 3), or, if the inverter is installed in an area with poor ventilation, the heat generated by said components will build up and cause potential premature component failures.
As the inverter compressor era becomes better established in the HVAC/R marketplace, there are several outstanding issues making widespread adoption less likely in the near future.
For one thing, the initial cost of cold climate inverter driven compressors featuring dense vapour injection make them less attractive to budget conscious homeowners and builders who continue to prioritize cost over long-term energy savings.
Another potential Achilles Heel is complexity. The process of adjusting compressor speed to maintain consistent indoor temperatures and superior humidity control means more sophisticated sensors and advanced control systems combined with line after line of proprietary software codes making diagnostics and repairs that much more challenging in the event of a malfunction.
Technicians and installers must learn to work with high DC voltage. Line set sizing requires strict adherence to manufacturer specifications related to tubing run and rise maximums, otherwise, oil management systems designed to ensure adequate amounts of oil is returned to the compressor sump will be impaired and will result in disastrous compressor failures.
The potential for considerably higher repair and maintenance costs does exist and cannot be ignored.
Our industry needs no more warnings about the shortage of qualified installers and technicians needed to make the inverter era work as advertised. Only a steady and ample stream of trade school graduates deciding to embrace a career in HVAC/R every year will make a difference in furthering the advance of the inverter era.
Added to the skilled labour challenge, manufacturers intend to introduce residential equipment charged with low global warming potential (GWP) “mildly flammable” A2L refrigerants by early 2025. Another round of training to familiarize the trade with A2L refrigerants coupled with the introduction of new safe handling techniques and new tools approved for use with A2Ls suggests contractors should start early; get your staff up to speed as soon as possible and continue remedial training into the future.
The multiple thorny issues of high initial cost, lack of competent HVAC/R technical staff, linked to an electrical infrastructure not nearly ready for full scale electrification means that the inverter era will, figuratively speaking, stagger into its own rather than take off like the scroll compressor era.
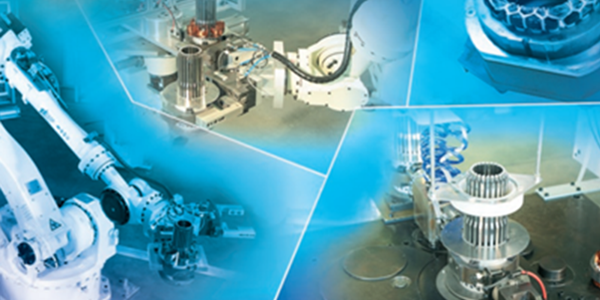
Six-Station Inner Winding Machine And it’s too bad, because as there are advantages and disadvantages to both inverter driven and conventional compressors, the benefits of comfort, durability, noise reduction, and energy efficiency are surely making inverter driven compressors a better choice for most residential heat pump and air conditioner applications. <>