Oct. 3—LAKE CRYSTAL — The robot remained focused on its assigned task throughout the ceremony Tuesday morning, swinging its welding arm from one target to the next, even as the human workforce at Truck Bodies and Equipment International celebrated its collaboration with Minnesota State University.
"It's a really good example of a university and industry partnership," said John Ruprecht, a member of the automotive and manufacturing technology faculty at MSU. Welding Arm

Ruprecht and MSU faculty colleague Kuldeep Agarwal were passing out certificates to roughly 60 TBEI workers, commemorating their successful completion of training in how to program a robotic welder. It's part of a years-long collaboration between the university, the state Department of Employment and Economic Development and the designer and manufacturer of dump truck bodies, trailers and other truck accessories.
The impetus for the collaboration was the labor shortage in south-central Minnesota, Agarwal said. If there are not enough workers, it's critical that those on hand be particularly well-trained to maintain production levels.
TBEI workers now have knowledge and experience in how to use a robot to do some of the welding tasks at the rural Lake Crystal plant, a strategy that could potentially expand in the years ahead even if the available workforce doesn't.
"If we can reduce the burden on actual welders, there can be kind of an alliance between the welders and robots to produce parts more cheaply," Agarwal said.
A $313,000 Minnesota Jobs Skills Partnership grant from DEED covered the analysis, expertise and training provided by the MSU faculty members in addition to the $100,000 cost of the MSU-owned robot stationed at the plant. The partnership's goal goes well beyond simply teaching the employees how to make a robotic welder do a job.
Instead, the initiative aims to provide TBEI with the ongoing ability to analyze where automation makes sense, where the specialized skills of human welders remain critical, how the choices might affect energy consumption, whether a particularly tedious task might be turned over to a machine and save a human worker from a repetitive stress injury and more.
The experienced staff at TBEI had plenty to teach the teachers, too, about how the robot should be instructed to complete a weld, such as flow rates and angle of attack, Ruprecht said.
"They had a lot of really keen insight into how the robots should be programmed," he said.
Some of the workers at the plant were initially skeptical about a robotic coworker, conceded Bill Kirtz, manufacturing manager for TBEI.
"Now, after they were able to put their hands on it and see how easy it was to use, they were excited," Kirtz said.
The company is, too. A second grant appears likely when the current one ends next summer.
"We're already considering writing a third one so we can keep this relationship going," he said.
TBEI, after using MSU's machine, is also contemplating taking the plunge with the purchase of a couple of production-line robots of their own as soon as next year. That's financially feasible for more and more manufacturers, according to Agarwal, who said robots that once cost close to $1 million apiece can now be had for about $100,000.
And Kirtz said it won't be a case of human welders teaching their future replacements how to do the job. It's more like training a new co-worker, and then setting them on their assigned job each day before the flesh-and-blood welders focus on their own tasks.
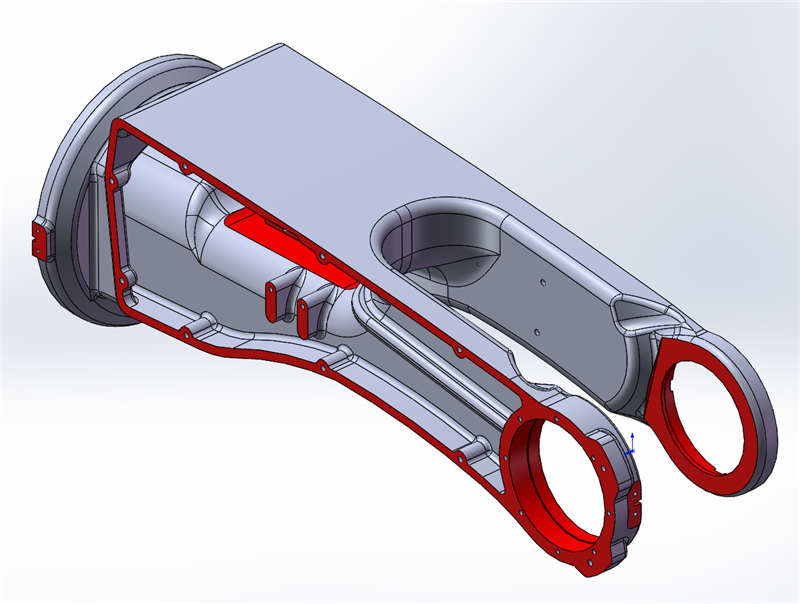
Robotic Arm For Welding Aluminum "What we're looking at is more of a 'weld buddy,'" he said.